The Process of Plastics Rotomolding: How It Works and Why It Matters
The Process of Plastics Rotomolding: How It Works and Why It Matters
Blog Article
Plastics rotomolding, or rotational molding, is a manufacturing process that's obtained immense reputation because of its ability to create resilient, hollow components with excellent precision. From large commercial tanks to small custom components, this approach is noted for its flexibility and efficiency. Under, we'll examine the main element benefits of Pockets Rotomolding and why it's develop into a preferred option for creating high-quality, hollow parts.
What is Pockets Rotomolding?
Rotomolding is a production procedure that requires heating plastic-type inside a spinning mold. This permits the molten plastic to coat the inner materials of the form uniformly, making empty parts with a seamless structure. The effect? An item that is not just sturdy but in addition amazingly adaptable, providing countless programs across industries.
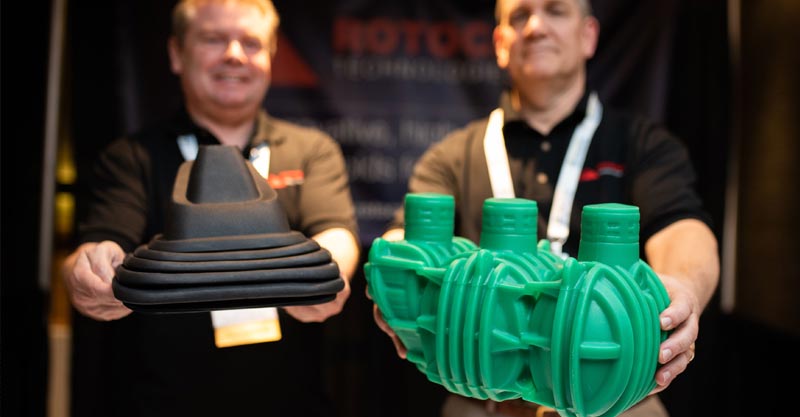
Crucial Benefits of Parts Rotomolding
1. Energy and Toughness
Among the standout benefits of pockets rotomolding is the unmatched longevity it offers. Rotomolded areas are created to tolerate severe problems, including large affects, hard climate, and substance exposure. This strength makes rotomolded pieces well suited for purposes in industries like automotive, agriculture, and construction.
The smooth, single-piece structure also contributes to the architectural strength of rotomolded products. Unlike other practices, you will find no joints or weak points, lowering the risk of breaks or leaks.
2. Cost-Effective Creation
Rotomolding is extremely cost-effective, specially when making big or complex worthless parts. The process needs relatively reduced tooling prices compared to different production techniques, such as injection molding or blow molding. That causes it to be particularly suited to small-to-medium creation runs without reducing quality.
Furthermore, the capability to make pieces with regular wall thickness decreases substance waste, optimizing cost-efficiency actually further.
3. Design Flexibility
The versatility of rotomolding opens the doorway to highly personalized designs. Whether it's intricate forms, undercuts, or various wall thicknesses, rotomolding enables companies to turn even the most complicated models in to reality. That mobility is important for industries that demand accuracy and flexibility in their components.
Further customization choices contain bumpy surfaces, embedded inserts, and also multi-layered areas for added warmth or strength.
4. Light However Strong
Rotomolded parts obtain the perfect stability between fat and durability. The worthless structure minimizes material application, ensuring items remain light while maintaining their architectural strength. That is particularly very theraputic for areas such as outside gear, tanks, or playground structures, where easy transport and installation are important considerations.

5. Eco-Friendly Production
Rotational molding can also be widely celebrated because of its environmental benefits. The method benefits in little product spend, as plastic components may frequently be reused or recycled. Additionally, producers may use eco-friendly materials to arrange with sustainability goals. This positions rotomolding being an increasingly appealing choice for companies seeking to cut back their environmental impact.
Why Plastics Rotomolding Stands Out
Materials rotomolding has changed the creation of sturdy, worthless parts by offering a unique combination of energy, cost effectiveness, and style flexibility. By leveraging this method, companies may offer high-quality areas that meet the particular needs of various industries while encouraging an eco-conscious approach to production.
If you are looking for a manufacturing process that produces easy longevity and unbeatable accuracy, rotomolding could be the answer.
Report this page