How Rotational Molding Is Used in Creating Durable and Complex Shapes
How Rotational Molding Is Used in Creating Durable and Complex Shapes
Blog Article
Rotational molding, commonly referred to as Rotomolding, has gained significant traction in the production business because of its versatility and efficiency. This method of making custom plastic products presents a variety of advantages, making it a chosen choice for suppliers catering to industries like automotive, agriculture, medical, and customer goods.
Usefulness in Design and Customization
One of many standout advantages of Plastics Rotomolding is their immense design flexibility. With this specific method, companies can create complicated shapes, standard wall thickness, and also double-walled structures without requiring complex tooling. That helps it be a perfect production selection for services and products like tanks, containers, industrial gear, and even outdoor furniture.
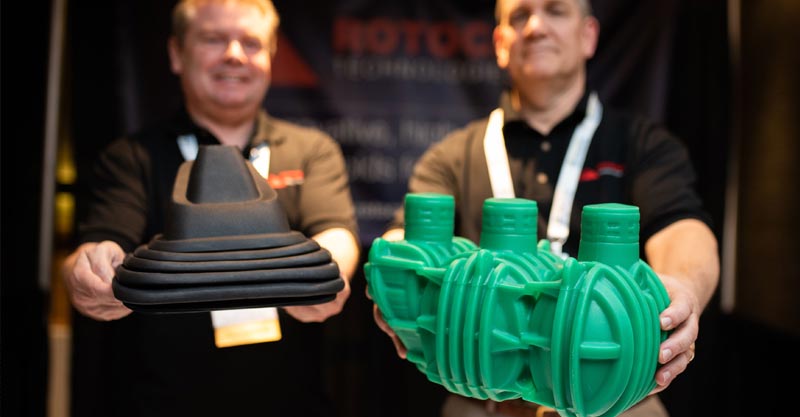
Rotomolding also allows for quick customization. Need your business emblem stuck into the product? Rotomolding can perform that. Want an uneven end? No problem. By playing with molds, suppliers may introduce colors, completes, and design facts which make your item unique.
Cost-Effective for Small Production Works
Unlike other plastic production techniques like treatment molding, rotomolding is less expensive for little manufacturing batches. The tooling price is somewhat lower since shapes don't must be strengthened to handle high-pressure programs, as noticed in other creation methods. That makes rotomolding an economical selection for businesses that do not involve bulk production.
More over, the slow heating and chilling cycle decreases material wastage, which is yet another cost-saving factor. Producers can use various resins to accommodate the necessary specifications, offering both flexibility and effectiveness in terms of natural product usage.
Longevity Meets Sustainability
Rotomolding doesn't only create sturdy plastic products—in addition, it aligns with rising sustainability goals. Services and products created applying this method are known for their unbelievable toughness and weight to tension, which is why they're frequently employed for water tanks, traffic barriers, and heavy-duty agricultural applications.
On top of that, rotational molding employs high-grade polyethylene, that will be recyclable. This can help reduce plastic waste without compromising the architectural quality of the products. Moreover, scrap substance developed during the molding method can usually be reused, rendering it a smarter selection for eco-conscious manufacturers.

Regular Quality and Efficiency
Reliability is still another noteworthy benefit of rotomolding. The procedure reduces the possibility of fragile areas frequently seen in different manufacturing methods. By maintaining even wall width and producing seamless areas, rotomolding guarantees that the ultimate solution matches structural and useful standards.
The reduced danger of defects equals a higher rate of customer satisfaction and fewer solution returns—an essential element for producers dedicated to quality assurance.
Rotomolding stands out as a powerful, inexpensive, and environmentally aware approach for providing custom plastic products. From its versatility and customization alternatives to its minimum waste manufacturing method, this method remains to make waves across industries that demand advancement and durability.
Report this page